Industry Educational Session - Linsinger smart Surface technology - The LINSINGER Group is once again proud to unveil another world-first innovation in rail profile management. - Sponsored by Linsinger
Tracks
Industry Sessions & Demos
Tuesday, April 16, 2024 |
1:45 PM - 2:15 PM |
Industry session : Hall 2a |
Details
Rails must withstand ever-increasing demands in standardized operation. These demands inevitably reach the limits of the rail material. As a result, rail defects and deformations occur on the rail head surface. Reprofiling worn rails using a milling machine from Linsinger GmbH is the right way to ensure a long-lasting rail network. With the Linsinger rail milling process, cracks that do not reach below the removal depth can be removed and the profile restored. The milling process requires a post-processing system due to acoustic effects. A polishing process is currently used but has some process-related disadvantages such as flying sparks, grinding dust and the of heat contribution into the real head. For this reason, Linsinger has now developed a post processing system which fulfills the tasks by means of a shot peening process. This so called Linsinger smart surface Technology is not just a post processing unit. The advantages are noise reduction, spark free, no grinding, no heat contribution into the rail head, introduction of residual compressive stress and homogenous surface. Especially the introduction of residual compressive stress could lead to a more resistant surface in the peened area against crack growth.
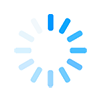